I am a fan of the Industrial Revolution and have worked in the industry since 2004. I have always been fascinated by the use of emerging technologies in industrial processes and have worked on various applications. In 2008, I even attempted to control industrial plants through the internet, though I was not familiar with the term “IoT” at that time. It wasn’t until I moved to Italy that I began to learn about IoT and its potential impact on industrial plants. During my research on the future of factories (FoF), I came across the concept of Digital Twins. At first, I was confused and wondered if it was referring to a simulator or something else entirely. In this post, I aim to clarify the differences between these two concepts, and hope you find it informative.
Digital Twin
A digital twin is a virtual replica of a physical object or system. It is a digital representation of a physical asset, process, or system that uses data and analytics to simulate and predict its behavior and performance in the real world. Digital twins can be used for a variety of applications, such as product design and optimization, predictive maintenance, process improvement, and performance monitoring. They can be created using a combination of data from sensors, IoT devices, and other sources, as well as computer-aided design (CAD) models and simulation tools. By creating a virtual model of a physical system, digital twins can enable businesses to make more informed decisions, improve efficiency, reduce costs, and increase productivity.
The key point in Digital Twin
The key point of digital twins is that they are virtual replicas of physical systems or processes that are continuously updated with real-time data from sensors, IoT devices, and other sources. This allows the digital twin to monitor, simulate, and predict the behavior and performance of the physical system, as well as to optimize design, maintenance, and performance.
Digital twins are used in a variety of industries, including manufacturing, healthcare, energy, and transportation, to improve efficiency, reduce costs, and increase reliability. By providing a virtual model of a physical system that can be monitored and optimized in real time, digital twins offer numerous benefits, including:
- Improved design and development: Digital twins allow designers and engineers to test and optimize a product or system in a virtual environment before it is built, saving time and resources and reducing the risk of design errors.
- Predictive maintenance: By monitoring the behavior and performance of a physical system in real-time, digital twins can predict when maintenance is needed, reducing downtime and improving reliability.
- Improved performance: Digital twins can optimize a system’s performance by simulating different operating conditions and identifying the best settings.
- Reduced costs: By optimizing design, maintenance, and performance, digital twins can help businesses reduce costs, increase efficiency, and improve profitability.
The key point of digital twins is to provide a virtual model of a physical system that can be continuously updated and monitored in real-time to improve efficiency, reduce costs, and increase reliability.
Simulator vs. Digital Twin
A simulator and a digital twin are similar in that they are both virtual models of a physical system or process. However, there are some key differences between the two.
A simulator is typically a mathematical model or computer program that simulates the behavior of a physical system or process in a virtual environment. It is often used for training or research purposes, such as to test different scenarios or understand a complex system’s behavior. Simulators typically do not use real-time data from sensors or other sources and may not be directly connected to the physical system they are simulating.
On the other hand, a digital twin is a virtual replica of a physical system or process continuously updated with real-time data from sensors, IoT devices, and other sources. It can be used to monitor, simulate, and predict the behavior and performance of the physical system, as well as to optimize design, maintenance, and performance. Digital twins are typically used in the industry for predictive maintenance, process optimization, and performance monitoring applications.
Real-time data from sensors or other sources would need to be integrated into the simulator model to convert a simulator to a digital twin. This data would be used to continuously update the model with the current state of the physical system and enable the digital twin to simulate and predict the behavior and performance of the system in real-time. Additionally, a digital twin would need to be connected to the physical system in order to monitor and control its operation. This connection could be established using IoT devices or other communication technologies.
Let’s talk about the advantages
The advantages of having a digital twin are numerous, including:
- Improved design and development: Digital twins allow designers and engineers to test and optimize a product or system in a virtual environment before it is built, saving time and resources and reducing the risk of design errors.
- Predictive maintenance: By monitoring the behavior and performance of a physical system in real-time, digital twins can predict when maintenance is needed, reducing downtime and improving reliability.
- Improved performance: Digital twins can optimize a system’s performance by simulating different operating conditions and identifying the best settings.
- Reduced costs: By optimizing design, maintenance, and performance, digital twins can help businesses reduce costs, increase efficiency, and improve profitability.
To implement a digital twin, data from sensors, IoT devices, and other sources is collected and fed into a computer model of the physical system. The model is then used to simulate the behavior and performance of the physical system and make predictions based on that data.
One example of the implementation of digital twin technology in industry is in the aviation industry. Aircraft engines are expensive and complex systems that require regular maintenance to ensure safe and efficient operation. Using digital twin technology, a virtual model of an aircraft engine can be created and used to monitor and predict the performance of the physical engine. By collecting data from sensors and other sources, the digital twin can simulate different operating conditions and identify potential problems before they occur. This allows maintenance to be scheduled more effectively and reduces the risk of unscheduled downtime, improving reliability and reducing costs. Digital twin technology is also being used in other industries, such as manufacturing, energy, and healthcare, to improve performance and reduce costs.
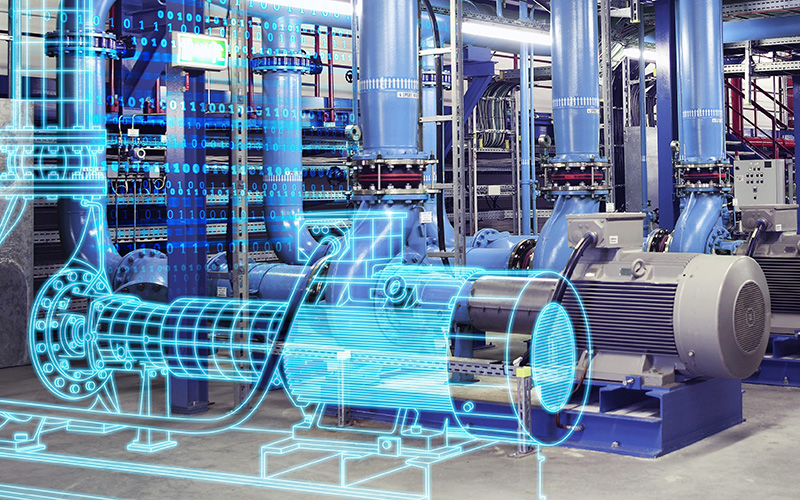
Machine learning impact on Digital Twin
Machine learning can be valuable in creating and maintaining a digital twin. One of the key benefits of a digital twin is the ability to use real-time data to monitor, simulate, and optimize the behavior and performance of a physical system. Machine learning algorithms can be used to analyze this data and predict future behavior and performance.
For example, in an industrial setting, machine learning could be used to analyze data from sensors and other sources to identify patterns and anomalies that could indicate potential problems or maintenance needs. The machine learning algorithm could then use this information to predict future performance and recommend actions to optimize performance and reduce downtime.
Machine learning can also be used to optimize the design and operation of a digital twin. For example, machine learning algorithms can analyze data from the digital twin and identify ways to improve efficiency, reduce costs, and optimize performance.
Another way machine learning can help with a digital twin is by improving its accuracy and reliability. Machine learning algorithms can be used to train the digital twin model on historical data, allowing it to make more accurate predictions about future behavior and performance. The more data the digital twin has to work with, the more its predictions will be more accurate.
Machine learning can help to create a more effective and efficient digital twin by providing insights and recommendations based on real-time data and historical trends.
Digital twin and Industry 4.0
Digital twins play a crucial role in Industry 4.0, which refers to the trend of using advanced technologies like IoT, machine learning, and AI to transform traditional manufacturing processes. By providing a virtual model of a physical system that is continuously updated with real-time data from sensors, digital twins offer several benefits to Industry 4.0, including:
- Improved efficiency: Digital twins can be used to simulate and optimize production processes, improving efficiency and reducing waste.
- Predictive maintenance: By monitoring real-time data from sensors, digital twins can predict when maintenance is needed, reducing downtime and maintenance costs.
- Enhanced collaboration: Digital twins can be used to share data and insights across different departments and locations, enabling more efficient collaboration and problem-solving.
- Faster innovation: Digital twins can be used to simulate and test new products and processes in a virtual environment, accelerating innovation and reducing the time and cost of physical prototyping.
- Increased automation: Digital twins can be used to automate and optimize processes, reducing the need for manual intervention and improving productivity.
In the future, digital twins are expected to play an even greater role in the factories of Industry 4.0. As more processes and equipment are connected to the Internet, the amount of real-time data available for digital twins will increase, enabling even more accurate and powerful simulations and optimizations. This will likely lead to greater efficiency, lower costs, and increased innovation in manufacturing. Digital twins could also enable new business models, such as offering products and services based on real-time monitoring and optimization of customer equipment.
Digital twins are a key enabling technology for Industry 4.0, and they are expected to shape the future of manufacturing by enabling more efficient, flexible, and innovative factories.
Conclusion
In conclusion, a digital twin is an emerging technology that significantly benefits various industries by providing a virtual replica of a physical system. It enables real-time monitoring, simulation, and optimization of industrial processes and equipment, resulting in improved efficiency, reduced downtime, and cost savings. A digital twin is expected to play a vital role in the future of Industry 4.0 by enabling more efficient, flexible, and innovative factories. Furthermore, with the integration of IoT and AI, digital twins can provide predictive maintenance and support for decision-making. The digital twin has the potential to revolutionize the manufacturing industry and transform the way we approach maintenance and innovation. As this technology advances, we can expect even more sophisticated applications and benefits for various industries.
I hope you found this article informative. Please stay tuned for our upcoming article on the Industrial Revolution and how emerging technologies are shaping our world.
A presto