Throughout my PhD studies, I had the opportunity to extensively research the future of the factory, with a particular focus on the topic of Industry 4.0. This was an incredibly exciting time, and I am grateful to Professor Claudio Demartini for guiding me on this journey. In this blog post, I would like to provide a summary of what Industry 4.0 entails and how it differs from traditional automation methods.
Let’s start from the beginning; The Industrial Revolution was a period of significant economic and social change between the late 18th and early 19th centuries, marked by the widespread adoption of new technologies and manufacturing processes. This period saw the transition from manual labor to machine-based manufacturing, significantly increasing productivity and efficiency. The Industrial Revolution was characterized by the introduction of machines and the development of new methods of production, which allowed goods to be produced faster and more cheaply.
The Second Industrial Revolution, also known as the Technological Revolution, occurred between the late 19th and early 20th centuries. This period saw the introduction of new technologies such as electricity, the telephone, and the internal combustion engine, which enabled greater levels of automation and productivity. The Second Industrial Revolution was characterized by the mass production of goods and the growth of large-scale corporations.
The Third Industrial Revolution, also known as the Digital Revolution, occurred in the late 20th century and early 21st century. This period saw the widespread adoption of digital technologies, such as personal computers, the internet, and mobile devices. The Third Industrial Revolution was characterized by the digitization of information and the development of new communication technologies, which enabled greater levels of connectivity and information exchange.
Industry 4.0 is the ongoing automation and digitization of manufacturing and other industries through the integration of advanced technologies such as the Internet of Things (IoT), artificial intelligence (AI), and big data analytics. Industry 4.0 represents a significant shift in the way that industries operate, moving from traditional, mass production models to more flexible, data-driven models that enable greater customization and agility. Industry 4.0 is characterized by the integration of advanced technologies that enable greater connectivity, automation, and data-driven decision-making. The ultimate goal of Industry 4.0 is to create smart factories and other facilities that can operate more efficiently and effectively, enabling companies to respond more quickly to changing market conditions and customer demands.
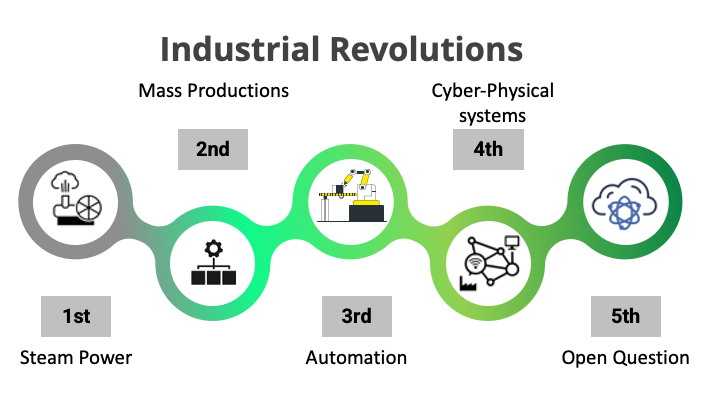
Industry 4.0
Industry 4.0, also known as the fourth industrial revolution, is a term used to describe the ongoing automation and digitization of manufacturing and other industries. It involves the integration of technologies such as the Internet of Things (IoT), artificial intelligence (AI), robotics, big data analytics, and cloud computing to create “smart” factories and other facilities that can operate more efficiently and effectively.
Industry 4.0 aims to transform traditional manufacturing processes by introducing new technologies that can monitor and analyze production in real-time, optimize supply chains, and enable the customization of products at scale. By doing so, it has the potential to increase productivity, reduce waste, improve quality, and create new business models and revenue streams.
Some examples of Industry 4.0 technologies include autonomous robots that can perform tasks without human intervention, 3D printing that can create complex parts on demand, and sensors that can monitor the condition of equipment and alert maintenance teams before failures occur. Overall, Industry 4.0 represents a significant shift in the way that industries operate and interact with their customers and suppliers.
There are several advantages to implementing Industry 4.0 technologies in manufacturing and other industries:
- Increased Efficiency: Industry 4.0 technologies can improve efficiency by automating processes and providing real-time insights into production. This can reduce the need for manual intervention, minimize downtime, and optimize production schedules.
- Improved Quality: Smart factories and other Industry 4.0-enabled facilities can use data analytics and other technologies to identify and address quality issues before they become major problems. This can help ensure that products meet customer requirements and reduce the need for rework.
- Cost Reduction: By optimizing production schedules and reducing the need for manual intervention, Industry 4.0 technologies can help reduce costs associated with labor, materials, and energy consumption.
- Customization: Industry 4.0 technologies can enable manufacturers to customize products at scale, using real-time data and analytics to make decisions about product design, production processes, and supply chain management.
- Innovation: By leveraging Industry 4.0 technologies, companies can create new business models and revenue streams that were previously impossible. For example, they can offer new services, such as predictive maintenance or pay-per-use models, or create new products that are tailored to specific customer needs.
Industry 4.0 technologies can help manufacturers and other industries to become more competitive and agile, allowing them to respond more quickly to changing market conditions and customer demands.
IoT and Industry 4.0
The Internet of Things (IoT) is a key enabler of Industry 4.0, and can help to develop it in several ways:
- Real-time Monitoring: IoT sensors and devices can be used to monitor production processes and equipment in real-time, providing manufacturers with insights into performance, utilization, and maintenance needs. This can help to optimize production schedules, minimize downtime, and improve overall efficiency.
- Predictive Maintenance: IoT devices can be used to collect data on equipment performance and condition, enabling predictive maintenance that can help to prevent breakdowns and minimize maintenance costs.
- Supply Chain Optimization: IoT devices can be used to track inventory, shipments, and other supply chain activities, providing manufacturers with real-time visibility into the status of their operations. This can help to improve supply chain efficiency, reduce costs, and enhance customer service.
- Product Customization: IoT devices can be used to collect data on customer preferences and behavior, enabling manufacturers to offer customized products and services that meet specific customer needs.
- Enhanced Quality Control: IoT sensors and devices can be used to collect data on product quality, enabling manufacturers to identify defects and other issues before they reach customers. This can help to improve product quality and reduce the need for rework.
IoT can help to enable Industry 4.0 by providing manufacturers with real-time data and insights that can be used to optimize production processes, reduce costs, improve quality, and enhance customer service.
What is the role of standardization in the future of factories?
Standardization is an important aspect of Industry 4.0, and can help to enable interoperability and avoid problems in integration and development. Standardization can help in several ways, including:
- Interoperability: Standardization can help ensure that different components and systems can work together seamlessly, even if they are from different manufacturers or suppliers. This can reduce the complexity and cost of integrating different technologies and systems, and enable greater flexibility and scalability.
- Efficiency: Standardization can help to simplify processes and reduce the need for customization, which can help to improve efficiency and reduce costs. By adopting common data models, protocols, and interfaces, companies can more easily integrate new technologies and systems into their operations, without the need for extensive customization or modification.
- Innovation: Standardization can enable innovation by providing a common platform for experimentation and development. By adopting standardized technologies and interfaces, companies can more easily collaborate with partners and suppliers to develop new products and services, without having to worry about compatibility or integration issues.
- Globalization: Standardization can help companies to expand into new markets and regions by enabling greater compatibility and interoperability. By adopting international standards, companies can more easily do business with partners and customers in other countries and avoid the costs and complexities of developing custom solutions for different markets.
RAMI 4.0, or Reference Architecture Model Industry 4.0, is a framework for designing and implementing Industry 4.0 solutions. It provides a standardized, modular architecture for Industry 4.0 systems to enable interoperability between different components and systems. The framework is based on a three-layer model, each representing a different aspect of an Industry 4.0 system: the Asset Layer, the Integration Layer, and the Business Layer. RAMI 4.0 aims to provide a common reference model that companies and organizations can use to design and implement Industry 4.0 solutions while promoting standardization and interoperability.
What is RAMI 4.0
RAMI 4.0, which stands for Reference Architecture Model Industry 4.0, is a framework for designing and implementing Industry 4.0 solutions. It was developed by the German government as part of its “Industrie 4.0” initiative, which seeks to promote the adoption of Industry 4.0 technologies in German manufacturing and other industries.
RAMI 4.0 provides a standardized, modular architecture for Industry 4.0 systems, to enable interoperability between different components and systems. The framework is based on a three-layer model, with each layer representing a different aspect of an Industry 4.0 system:
- The Asset Layer: This layer represents the physical assets of an Industry 4.0 system, such as machines, sensors, and other devices. The assets are represented in a standardized format that allows them to be easily identified and integrated into the system.
- The Integration Layer: This layer represents the communication and integration infrastructure of an Industry 4.0 system, including protocols, interfaces, and data models. The layer is designed to enable interoperability between different components and systems, allowing data to be exchanged and analyzed in real-time.
- The Business Layer: This layer represents the business processes and applications that drive an Industry 4.0 system, including production planning, quality control, and supply chain management. The layer is designed to enable flexible, adaptive processes that can respond quickly to changing market conditions and customer needs.
RAMI 4.0 provides a standardized, modular framework for designing and implementing Industry 4.0 systems, with the goal of enabling interoperability, flexibility, and scalability. By adopting RAMI 4.0, companies can more easily integrate Industry 4.0 technologies into their operations and leverage the benefits of digitalization and automation.

To developing RAMI 4.0 in Industry 4.0 involves several key steps, including:
- Standardization: Companies and organizations must adopt standardized data models and interfaces to ensure interoperability between components and systems. This can help to reduce integration costs and complexity and enable greater flexibility and scalability.
- Collaboration: Collaboration between different stakeholders is essential for developing RAMI 4.0 in Industry 4.0. This includes manufacturers, software vendors, system integrators, and other organizations that play a role in designing, implementing, and maintaining Industry 4.0 systems.
- Adoption: RAMI 4.0 can only be effective if it is adopted by a wide range of companies and industries. This requires education and awareness campaigns to help stakeholders understand the benefits of Industry 4.0 and the role that RAMI 4.0 can play in enabling digitalization and automation.
- Innovation: Industry 4.0 is a rapidly evolving field, and RAMI 4.0 must be able to adapt to new technologies and use cases. Innovation is, therefore critical for the ongoing development of RAMI 4.0 in Industry 4.0, and stakeholders must be willing to experiment with new approaches and solutions.
- Security: As Industry 4.0 systems become more interconnected and data-driven, security becomes an increasingly important consideration. RAMI 4.0 must therefore include robust security protocols and mechanisms to ensure data and systems’ confidentiality, integrity, and availability.
Developing RAMI 4.0 in Industry 4.0 requires a collaborative and iterative approach that considers the evolving needs and challenges of different industries and stakeholders. By adopting RAMI 4.0, companies can more easily design and implement Industry 4.0 solutions that are interoperable, flexible, and scalable.
Summary
Industry 4.0 is the automation and digitization of manufacturing and other industries by integrating advanced technologies such as the Internet of Things (IoT), artificial intelligence (AI), and big data analytics. Standardization is a critical aspect of Industry 4.0, which can help enable interoperability, avoid problems in integration and development, and drive innovation and efficiency. RAMI 4.0 is a framework for designing and implementing Industry 4.0 solutions, which provides a standardized, modular architecture for Industry 4.0 systems to enable interoperability between different components and systems. Machine learning is another key aspect of Industry 4.0, which has the potential to transform manufacturing and other industries by enabling greater automation, optimization, and customization.
A presto